Textile Recycling
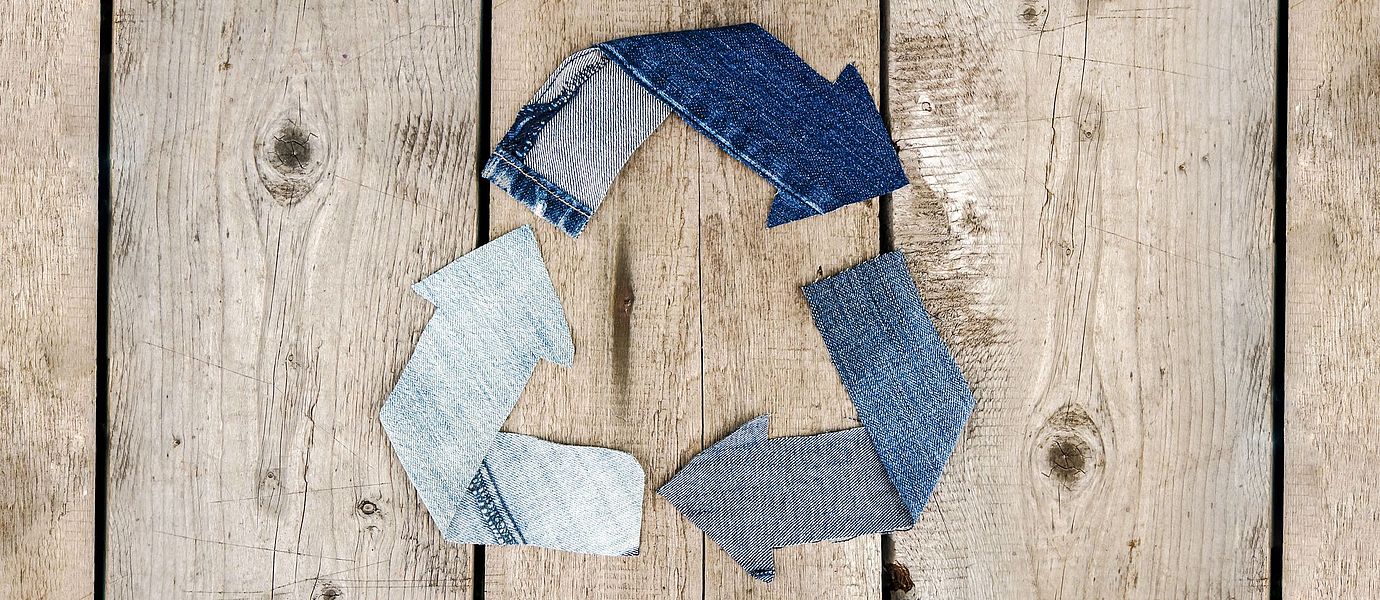
How can the current linear “take-make-waste” model of the textile industry be transformed into a circular system? Rieter is innovating the spinning process to support this transformation. The company enables spinning mills to create high-quality yarn from mechanically or chemically recycled textile waste. A classification system for recycled fibers helps the spinning industry estimate the final yarn quality based on the parameters of recycled fibers. And this is only the beginning.
Clothing is made, worn, and eventually discarded. Less than 1% of these used textiles are recycled in a closed-loop system, where they are transformed into new fashion items of equal value. This linear “take-make-waste” model is harmful to the environment.
Rieter’s cutting-edge fiber recycling technology paired with unparalleled textile expertise are essential in helping the textile industry achieve the breakthroughs it needs to close the loop and give rise to a more circular future.
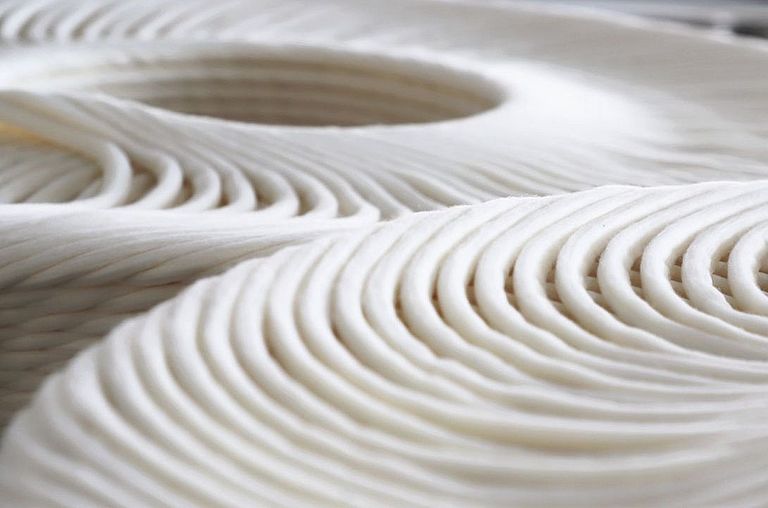
Mechanical recycling of textiles: tried, tested and trusted
The most widely used method of textile recycling is mechanical recycling, which has been in use for decades. Textiles are first torn into smaller fragments and then into fibers before they are spun into new yarns. The drawback is that mechanical recycling results in a high proportion of short fibers which impairs yarn quality in the spinning process.
Rieter is investing into research to overcome the challenges posed by the high share of short fibers with a particular focus on the ring and compact spinning processes as they are the predominant spinning technologies for standard yarns. The company has launched three tools to help customers achieve a yarn quality from mechanically recycled cotton fibers that matches the standard of an average carded ring yarn made from 100% virgin cotton: pre-carding for full cleaning, combing to improve yarn quality, compacting to add the finishing touch.
By contrast, rotor spinning is better suited for applications that use materials with higher short-fiber content, and customers have been counting on Rieter’s rotor spinning technology for recycling applications for decades.
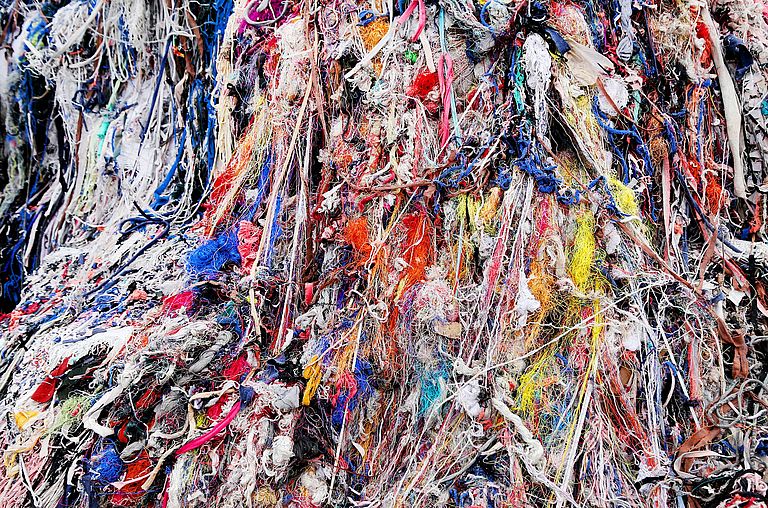
Classification system for spinning recycled fibers
To help spinners realistically assess their production targets based on the fibers used, Rieter has introduced a recycling classification system to the market. The classification highlights the key parameters after the tearing process, including short-fiber content, average fiber length and the share of long fibers that exceed the 5% threshold. Spinners can determine the most suitable process and which yarn evenness and degree of fineness they can achieve with the given material.
Chemical recycling of textiles: a revolution in the making
Rieter helps customers develop breakthrough yarns that use sustainable chemical manufacturing processes. Fiber company Spinnova, for example, has set up an R&D spinning line equipped with Rieter machines to manufacture a yarn without harmful chemicals, pollution or waste.
Rieter also helped the US specialty chemicals company Eastman to develop the Naia fiber, which is produced in a closed-loop process from pulp sourced from sustainably farmed pine and eucalyptus forests.
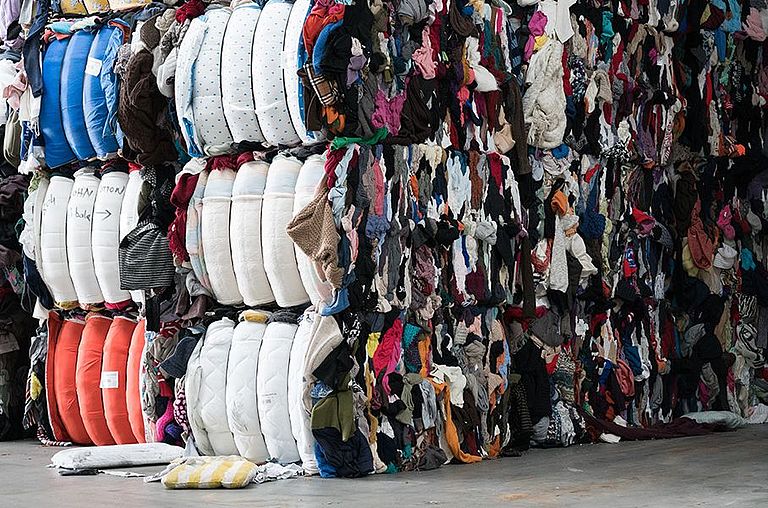
Collaborating for more circularity in textile production
Rieter works with fiber producers to better understand and optimize the spinnability of recycled fibers. For chemically recycled fibers, the company works with Birla, an established viscose producer in India, and for mechanically recycled fibers with Recover, a producer of recycled cotton fibers based in Spain. The company is researching the environmental footprint of yarns with the German Institute for Fiber Research in Denkendorf.
The Circular Economy - A Definition
The Ellen MacArthur Foundation, a leading think tank in this sector, estimates that if the trend remains the same, over 150 million tons of garments will be discarded or incinerated annually by 2050.
In a “circular economy”, according to the Ellen MacArthur Foundation, materials are recycled any number of times, waste and pollution are avoided, and nature is regenerated. The Rieter Group continues to develop recycling technologies and expertise to support the textile industry on this route.