The Rieter ring spinning system with different options of compacting devices is renowned for consistently high yarn tenacity, low hairiness and maximum flexibility. Customers who opt for this system also benefit from lower production costs compared to a spinning mill that uses machines from other Chinese suppliers. This fully automatic and intelligent Rieter ring spinning system covers all processes from blowroom through to packaging and palletizing and offers round-the-clock availability, so production output can be increased and personnel costs can be reduced. The cash flow generated demonstrates the outstanding economy of this perfectly synchronized, complete system.
Ring/Compact-Spinning System
On the way to ten operators per 10 000 spindles – an example for China- Productive and reliable process
- Highest level of flexibility
- Lowest total production costs
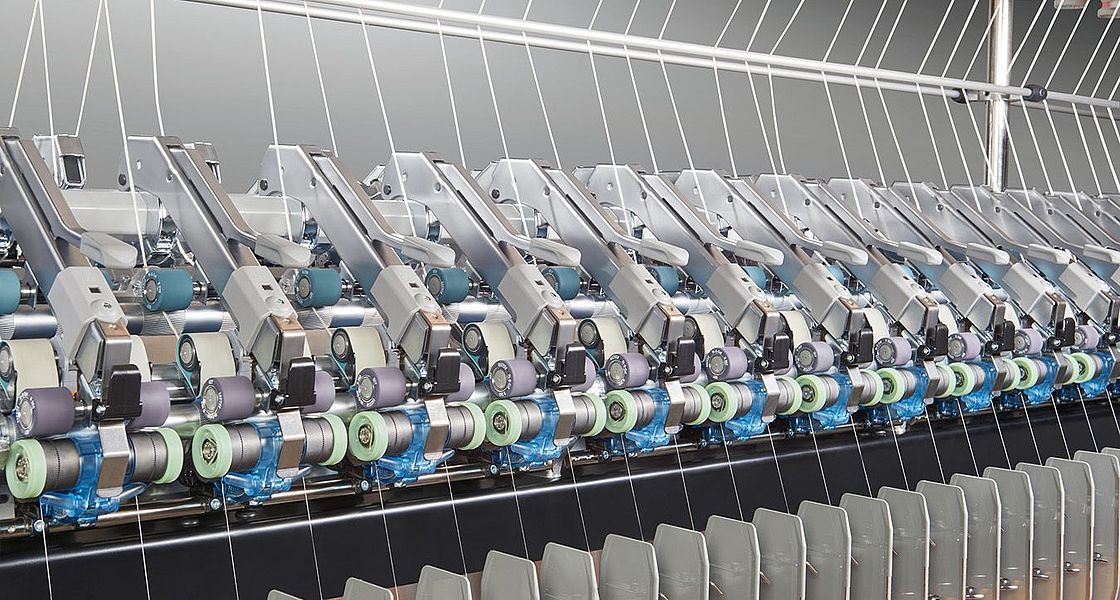
Chinese compact spinning system for combed cotton yarn
This example presents a compact-spinning system that uses medium staple cotton to produce a combed cotton yarn with a count of Ne 40. A spinning mill from a Chinese supplier was used for comparison. The unique yarn characteristics, such as the low hairiness of the compact yarn produced on a ring spinning machine G 38 with the compacting device COMPACTdrum, can lead to a higher yarn price. However, the case study does not take this benefit of using Rieter machines into account and is instead based on raw-material prices and yarn prices for both systems being the same.

Additional cash flow of the Rieter system: approx. CNY 7 million per year
- Raw-material utilization
+ 1-2%
- Energy consumption
- 6%
- Personnel requirement
- 30%
- Productivity
+ 20%
The Rieter Solution
Basis of calculation
Yarn production: 925 kg/h
Raw-material costs: 15 CNY/kg
Energy costs: 0.7 CNY/kWh
Operator wage: 26.75 CNY/h, plus 50% overhead costs
Country: China
Flexibility
The ring spinning machine G 38 with compacting device COMPACTdrum offers spinning mills the highest possible level of flexibility: Switching between ring yarn and compact yarn has never been so easy.
The yarn produced using the compacting device COMPACTdrum is impressive thanks to its high tenacity and offers a remarkable new dimension in hairiness reduction, particularly for long hairs. This creates new possibilities for spinning mills when it comes to yarn design.
The G 38 enables yarn parameters to be easily changed on the operating unit thanks to the proven fully electronic drafting system.
Energy consumption
Energy-efficient drive concepts and innovative machine components throughout the process generate energy savings of 6% – all the while maintaining the highest possible levels of productivity. The blowroom line VARIOline with the option ECOrized plays a significant part in this. It reduces the energy consumption of the pneumatic fiber transport used throughout the blowroom system by 30%. The ring spinning machine G 38makes the largest contribution to reducing the energy consumption of the Rieter system. This reductions results from the double-sided suction, energy-efficient elements and motors as well as energy-saving spindles and an energy-saving spindle drive.
Personnel requirement
The Rieter system requires 30% fewer operators. The reason for this are automation solutions such as the roving bobbin transport system, the cone packaging system from Rieter partners and the piecing robot ROBOspin on the G 38 The individual spindle monitoring system ISM premium is standard on G 38 machines. It is an operator guidance system for improved efficiency, resulting in fewer operators and/or increased productivity (spindle speed). Moreover, user-friendly machines contribute to this saving as part of an overall concept. Rieter systems are able to achieve the same level of production with fewer machines.
Raw material utilization
The Rieter system can be used to achieve raw-material savings of 1 to 2% compared to a spinning mill with machines from other Chinese suppliers. In addition to high yarn quality, the reduction of waste is an essential factor for an economical compact spinning process with combed cotton. High-quality technology components on the comber E 86 and extremely precise machine settings reduce noil extraction while maintaining the same yarn quality.
Space requirement
The high productivity of Rieter machines means fewer machines are required. This saves space compared to a spinning mill with machines from other Chinese suppliers. In the case study mentioned above, the Rieter spinning mill requires 20% fewer ring spindles than the spinning mill from other Chinese suppliers. Space-saving machine concepts lead to a more compact spinning mill layout. This means much less space is required, and therefore significantly lower building investments and lower maintenance costs.
Additional cash flow
The total production costs calculated for the Rieter system for the combed compact spinning process are lower than a solution from other Chinese suppliers. This calculation includes the raw-material utilization, energy and personnel costs, the sales of yarn and noil and ongoing operations costs. Customers who invest in the Rieter compact-spinning system as per our example generate an approx. CNY 7.3 million higher cash flow per year at the same production volume than customers who choose a spinning mill with machines from other Chinese suppliers.
The system partner
A complete Rieter system is established on Rieter’s expertise throughout the entire spinning process: from processing raw material to yarn. Rieter offers all four end spinning processes and provides professional advice on the optimal spinning technology. Furthermore, experts provide support with yarn marketing and offer a wide range of services. The entire spinning mill is networked and controlled from a single platform with ESSENTIAL – Rieter Digital Spinning Suite. This guarantees high quality and optimal efficiency, both now and in the future.