The Rieter ring spinning system is renowned for energy-saving and flexible production of yarns of the highest quality. No matter whether it is standard yarns of any yarn count, slub yarns or fancy yarns, core yarns or twin yarns, a ring spinning system offers the most flexible solution for every spinning mill. The cash flow generated by the system selected here demonstrates significantly improved cost efficiency over the entire system, which is perfectly synchronized and is supplied from one source.
Ring Spinning System
Spin high-quality ring yarns economically and flexibly- Consistently high yarn quality
- High energy savings
- Reduced personnel requirement
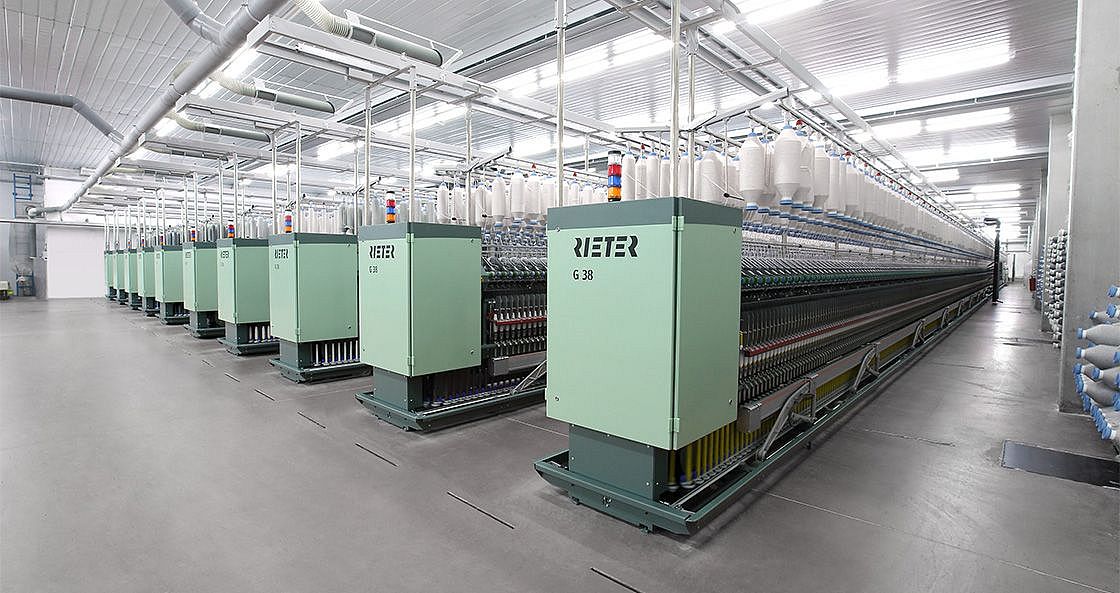
Ring spinning system for denim yarn
This example consists of a ring spinning system that uses short staple cotton to produce a fancy yarn with yarn count Ne 14 for denim fabrics. A “mixed spinning mill”, which is equipped with machines from two different manufacturers, was used for comparison.

Additional cash flow with the Rieter system: around USD 310 000 per year
- Space requirement
-10%
- Raw material utilization
+0.3%
- Energy consumption
-10%
- Personnel requirement
-3%
The Rieter Solution
Basis of calculation
Yarn production: 2 078 kg/h
Raw material costs: 1.70 USD/kg
Energy costs: 0.074 USD/kWh
Energy consumption
Energy-efficient solutions and a high production capacity generate energy savings of 10% across the process. The blowroom line VARIOline with the option ECOrized plays a significant part in this. It reduces the energy consumption of the pneumatic fiber transport throughout the blowroom system by 30%. High production output, energy-efficient drives, and innovative machine components on the card C 80 also lead to lower energy costs per kilogram of card sliver produced. The ring spinning machine G 38 with double-sided suction, energy-efficient elements and motors as well as energy-saving spindles and an energy-saving spindle drive make the largest contribution to the reduced energy consumption of the Rieter system.
Personnel requirement
The Rieter system requires 3% fewer personnel. In addition, Rieter systems are able to achieve the same level of production with fewer machines. Automation solutions such as the fully automatic roving frame F 40 with the fastest doffer on the market, the roving bobbin transport system SERVOtrail and user-friendly machines all contribute to this saving as part of an overall concept.
Raw material utilization
Fiber waste is a key factor in creating an economical ring spinning process. Low raw material loss is achieved in the blowroom line VARIOline thanks to the optimum combination of microtufts, the function VARIOset and progressive cleaning. On the high-performance card C 80, the maximum technological cross section and the pre- and post-carding zones that can be equipped individually ensure excellent raw material utilization. To summarize, raw material savings of 0.3% can be achieved with a Rieter system compared to a “mixed spinning mill”.
Space requirement
The high productivity of Rieter machines allows a reduction in the number of machines, thus saving a lot of space compared to a process using a “mixed spinning mill”: In the case study mentioned above, the Rieter spinning mill requires five cards, one draw frame and 5% fewer ring spindles than the “mixed spinning mill”. Space-saving machine concepts lead to a compact spinning mill layout. This allows space savings of approximately 10% and therefore significantly lower building investments and lower maintenance costs.
Additional cash flow
Taking raw material utilization, energy and labor costs, interest rates and ongoing operating costs into consideration, the total production costs calculated for the Rieter system for the ring spinning process are significantly lower than a solution from a mix of suppliers. This means that customers who invest in the Rieter ring spinning system as per our example generate an approximately USD 310 000 higher cash flow per year at the same production volume than customers who choose a “mixed spinning mill”.
The system partner
A complete Rieter system is established on Rieter’s expertise throughout the entire spinning process: from processing raw material to yarn. Rieter offers all four end spinning processes and provides professional advice on the optimal spinning technology. Furthermore, experts provide support with yarn marketing and offer a wide range of services. The entire spinning mill is networked and controlled from a single platform with ESSENTIAL – Rieter Digital Spinning Suite. This guarantees high quality and optimal efficiency, both now and in the future.