Energy Efficiency
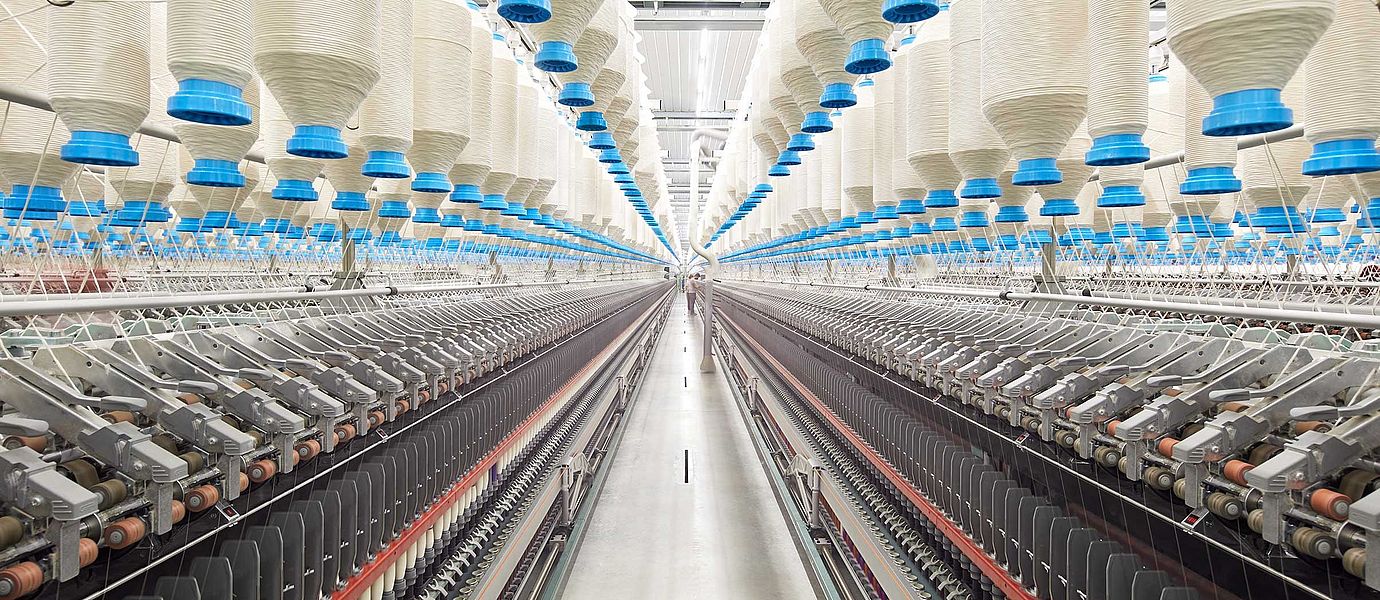
Energy efficiency is a hallmark of Rieter spinning systems. Climate change and rising energy costs require decisive action. That is why Rieter is setting measurable targets for 2030.
Energy efficiency in focus
For decades now, Rieter engineers have placed great emphasis on energy efficiency when developing new machines. This includes all machines relevant to the spinning process.
However, the greatest potential for energy savings is in the end spinning process. Spinning machines consume around 60% to 80% of the energy required for yarn production. The finer the yarn, the greater the motor speed and hence the higher the energy consumption. This applies above all to ring spinning machines and compact-spinning machines, which are used for finer yarns. Air-jet spinning machines require both electrical and compressed air energy.
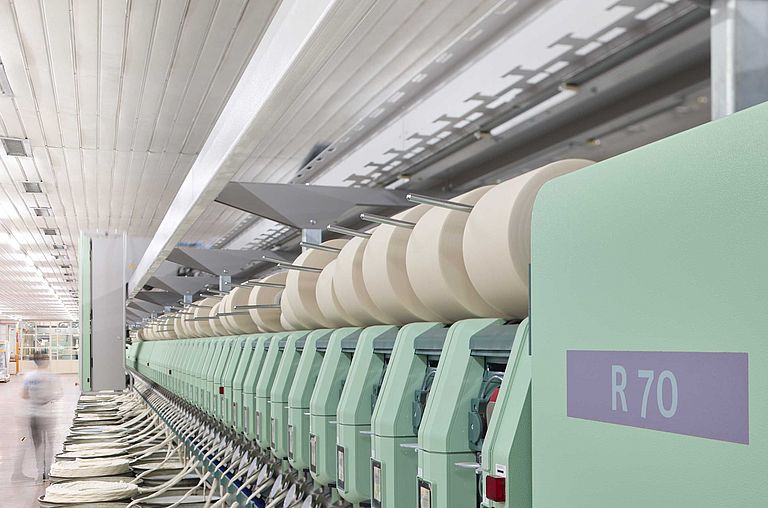
In comparison with the other three spinning technologies, the rotor spinning machine requires the least energy per kilogram of yarn. Since 2000, compared to today, Rieter has significantly reduced energy consumption for the production of 100 kg of Ne 30 viscose yarn: by 37% for the ring spinning system and by 54% for the rotor spinning system. For the air-jet spinning process, Rieter succeeded in reducing energy consumption by 69% since 2008.
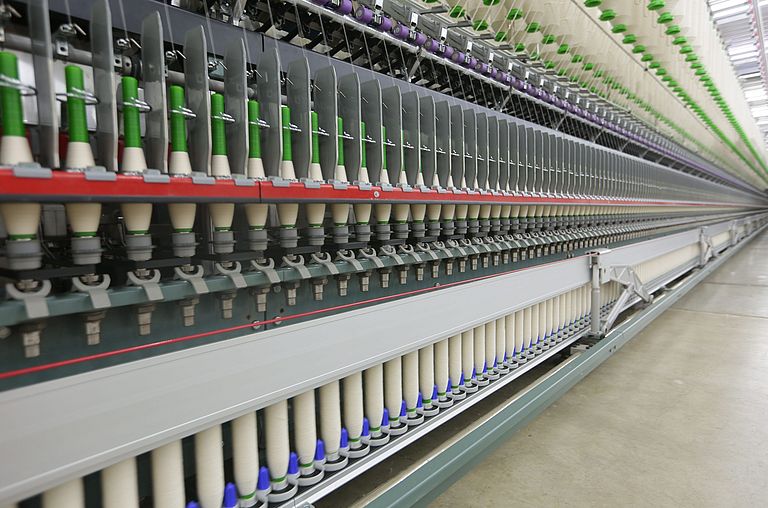
2025, 2030: Moving forward with ambition
The consumption of ring and air-jet spinning systems will be reduced by another 15% and 16%, respectively, by 2025, and 22% by 2030 compared to 2021. This will be accomplished mainly through energy-saving technologies and enhancements to all machines involved in the process. The new air-jet spinning machine J 70 also plays an important role here. The energy consumption of the comparatively highly efficient rotor spinning system will be reduced 2% by 2025 and another 5% by 2030.
The following examples illustrate Rieter's efforts to optimize machines and systems, particularly with regard to energy consumption.
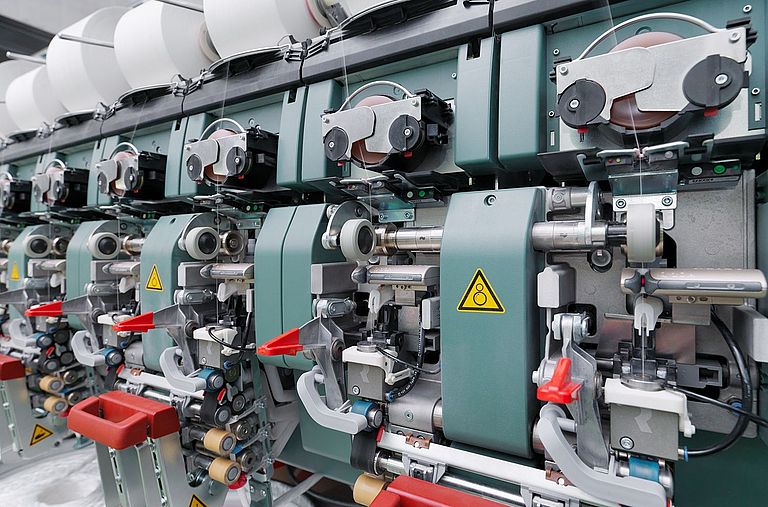
Innovating for more efficiency
Air-jet spinning is still a relatively novel technology. Its high productivity and the unique characteristics of the yarns will contribute to its strong growth in the coming years. In addition to the electrical energy for the drives and the exhaust system, the air-jet spinning machine requires compressed air for imparting twist during yarn formation.
The integration of an efficient suction system and energy-saving drives in the latest air-jet spinning machine J 70 has led to a 3% reduction in electricity usage per kilogram of yarn when compared to its predecessor. Furthermore, the J 70 boasts a 5% reduction in compressed air consumption per kilogram of yarn. This is achieved through higher delivery speeds with the same compressed-air consumption and lower inlet pressure. The fact that the J 70 runs robustly also in fluctuating ambient conditions is highly appreciated in humid and hot regions. Maintaining an optimal spinning climate in the mill consumes an enormous amount of energy.
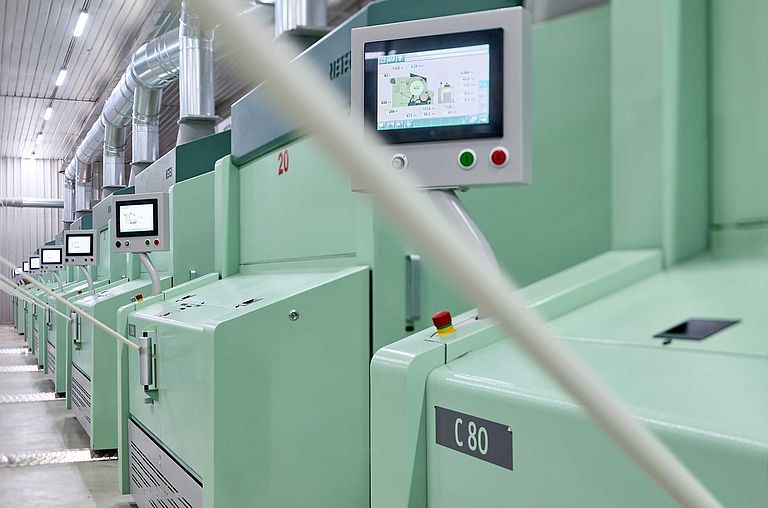
Efficient through and through
The card is an integral part of any spinning system. It breaks down fiber tufts into single fibers and processes them in parallel. It accounts for up to 15% of the energy consumed in the spinning process. The current card C 81 is central to achieving the 2025 efficiency targets.
It requires half as much energy as the card C 51 model from the year 2000. At the same time, the C 81 produces 40% more fiber sliver than its direct predecessor. This means that a modern spinning mill requires fewer cards for the same production output. This reduces energy consumption and therefore also lowers production costs.
Efficiency improvements
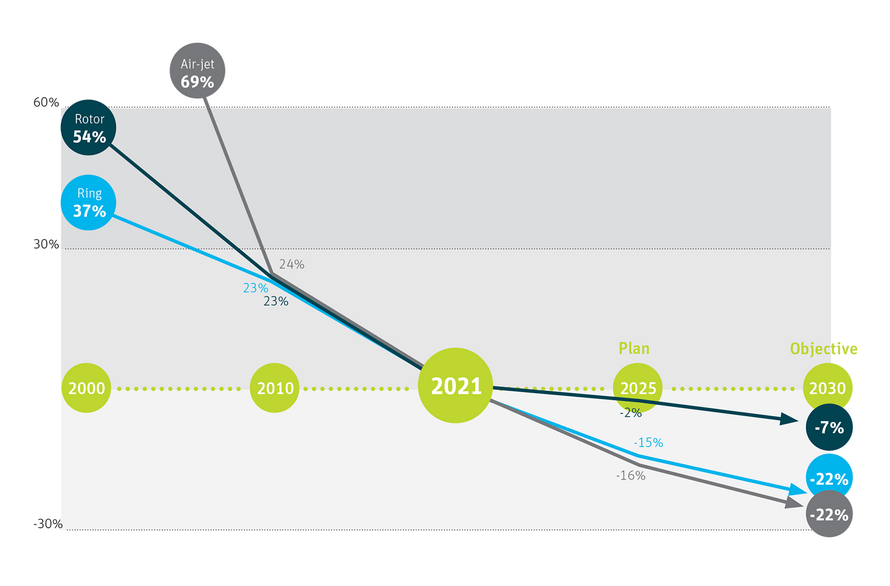
Energy efficiency of the spinning systems
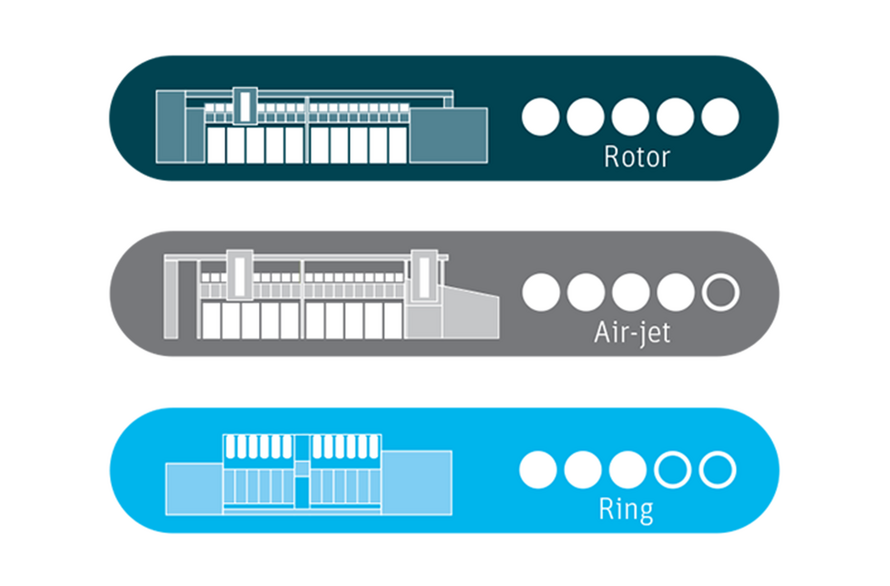
CO2 in the wider fashion industry
The fashion industry is responsible for around 4% of global greenhouse gas emissions. The report “Fashion on Climate” (2020)1 predicts that, without additional reduction measures, this figure could increase by one third by 2030. According to the study, yarn production accounts for around 8% of the industryʼs total emissions. Yarn production thus accounts for 0.32% of global greenhouse gas emissions. Although this figure is relatively small compared to other sectors, Rieter firmly believes that every contribution to reducing emissions is important. In times of rising energy costs, energy efficiency also enhances the competitiveness of spinning mills.
1 McKinsey and Global Fashion Agenda. (2020). Fashion on Climate.