Increasing Productivity with Smartjet Winding Upgrade
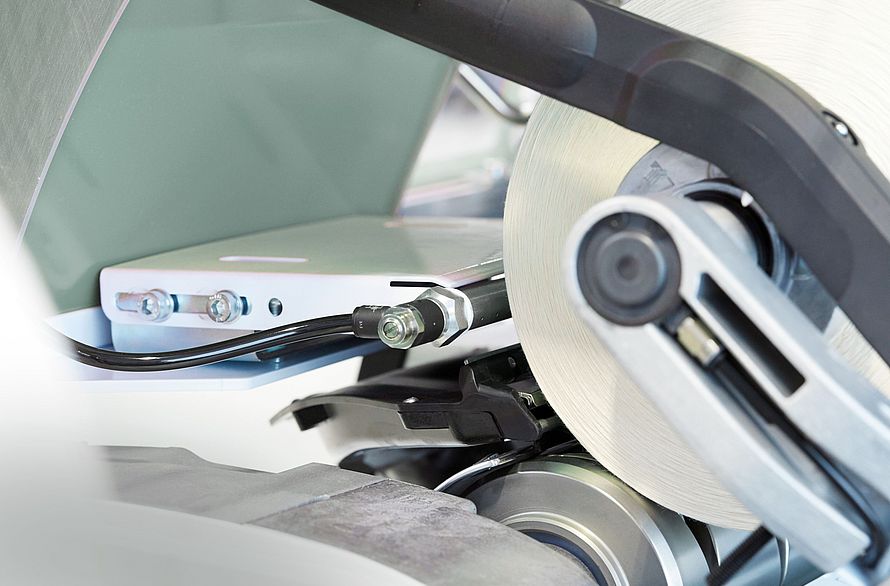
The Smartjet upgrade installed in the doffer unit helps improve the efficiency of the upper yarn search.
Viking Textiles Pvt. Ltd., India, increased its yarn production by 1% thanks to the Smartjet upgrade on their three winding machines Autoconer 6. The Smartjet power nozzle helps to increase the efficiency of the suction nozzle’s upper yarn search and pick-up from the package. This reduces the operator’s workload in attending the packages during red light stoppages of the winding units.
The Challenge
Viking Textiles Pvt. Ltd., India, are well-known for their quality knit-wear inner garments and produce approximately 3 000 tons of compact-combed hosiery yarn annually at their spinning facility. The customer operated three Autoconer 6 type RM (round magazine) with 60 drums each. One operator handled 40 drums. Operators are responsible for feeding the full cops to the round magazine and attending to packages where the suction nozzle cannot identify and pick the yarn end from the package for piecing. This additional task results in delays in attending the idle drums, which in turn leads to an increased operator workload.
The Solution
The Rieter After-Sales team installed the Smartjet upgrade on the doffer unit of the three Autoconer 6. This upgrade consists of a unique power nozzle used in the latest automatic winding machine Autoconer X6. Smartjet helps increase the efficiency of the upper yarn search and pick-up by the suction nozzle. Before a winding position activates a red light because it cannot identify a yarn end from the package, it sends the signal to the doffer unit. The Smartjet power nozzle efficiently supports the upper yarn search, thereby increasing the success rate of the upper yarn pick-up during the winding unit cycle process.
The Customer’s Benefits
The Smartjet upgrade has increased yarn production output by up to 1% due to improved machine efficiency. The frequent stoppage of the winding position and manual interventions are eliminated as the yarn pick-up from the package is more efficient. This results in a significant reduction in workload as they can concentrate only on the task of refilling the full bobbins into the round magazine. Process reliability is also improved as operators no longer need to touch the packages.
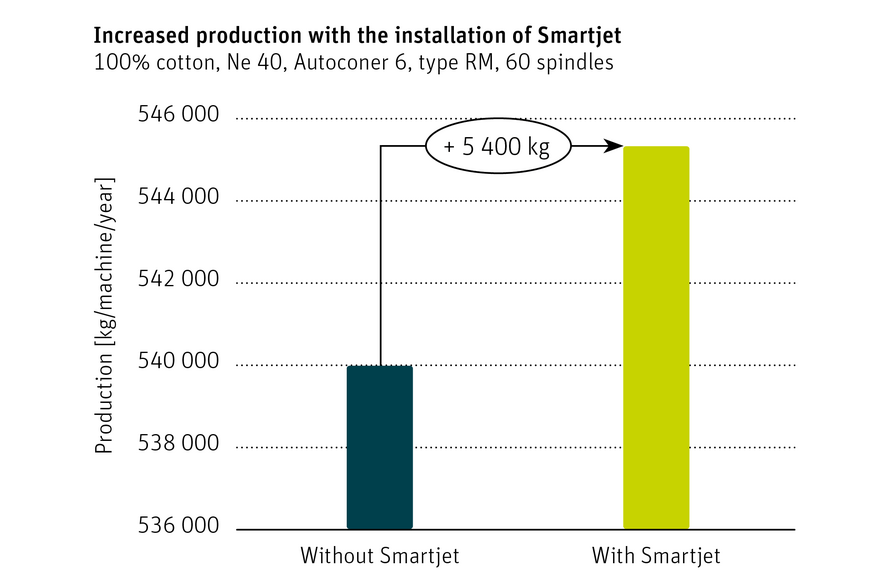
Smartjet has been installed in our three Autoconer 6 machines as a retrofit. After the installation of Smartjet, the operator's workload is reduced and the resources are optimized and utilized effectively. We are very happy that we could also increase the yarn production.Natarajan R, General Manager of Viking Textiles Pvt. Ltd., India
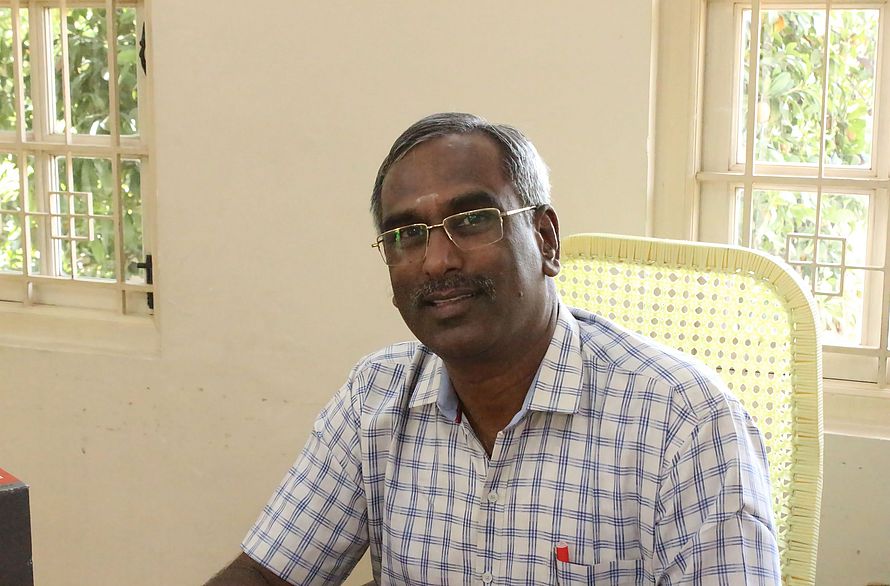