Increasing Production and Reducing Costs with Smartjet
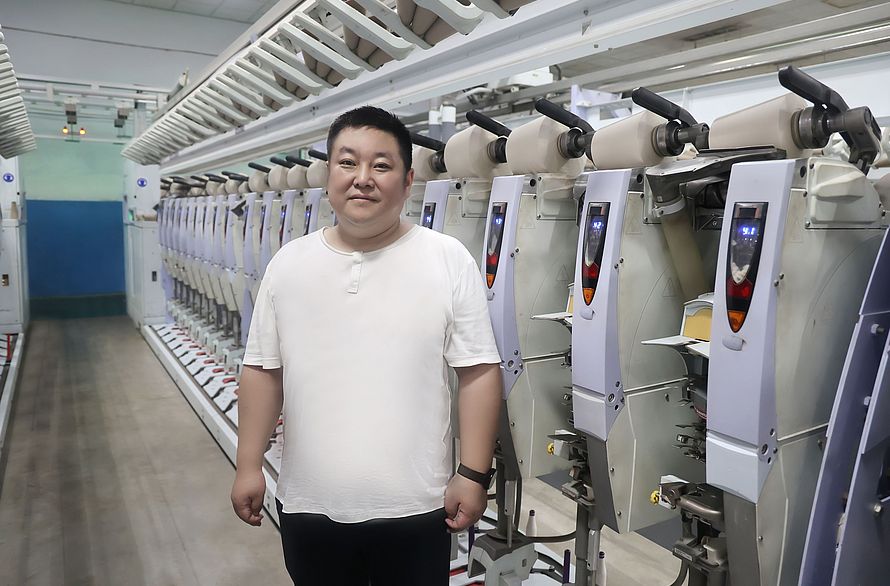
Wang Ping, Chief Engineer at Wugang Yinglong Group, is happy about the improved productivity and reduced energy costs made possible by the Smartjet conversion.
Facing intense competition and the need to maintain high-quality yarn production, Wugang Longshan Textile Technology Co. Ltd. partnered with Rieter to implement the innovative Smartjet power nozzle technology for their automatic winding machine Autoconer X5. This upgrade boosted machine efficiency by up to 3%, reduced operator workload and cut conversion costs, enabling Wugang Longshan Textile Co. Ltd. to strengthen their market position.
Rieter’s customer, Wugang Longshan Textile Technology Co. Ltd., located in Pingdingshan, Henan, China, operates with a substantial capacity of 360 000 spindles. Founded in 1988, it is a leading supplier of high-quality yarn in the market. Wugang Longshan Textile Technology Co. Ltd. is a subsidiary of Wugang Yinglong Group which has a total capacity of 700 000 spindles and specializes in producing compact cotton yarn in a yarn count range of Ne 32 to Ne 80, with an annual output of 60 000 tons of weaving and knitting yarn. Their average yarn count is Ne 45, and they consume around 70 000 tons of cotton annually. Additionally, they operate 2 160 rotor spinning units.
Coping with challenging market dynamics
In the face of intense competition and declining yarn prices, Wugang Longshan Textile Technology Co. Ltd. was looking for upgrades and conversions to reduce operational costs. They aim to be cost competitive without compromising on yarn quality.
Increased machine efficiency lowers conversion costs
Rieter’s after-sales team worked closely with Wugang Longshan Textile Technology Co. Ltd. to understand their specific challenges and needs. In March 2024, the Rieter team installed Smartjet conversions on three winding machines Autoconer X5. This upgrade included introducing additional parts to enhance machine performance.
The installation of the first batch of Smartjet power nozzles on the existing doffer unit significantly reduced downtime and the frequency of red lights on the machines. Smartjet functions as a search device, improving the success rate of upper yarn end manually searches by 51%. This technology supports the suction nozzle in picking up upper yarn ends that would otherwise be missed. The increased efficiency in yarn end searches translates directly to higher machine efficiency and reduced downtime. Impressed with the initial results, Wugang Longshan Textile Technology Co. Ltd. ordered the Smartjet upgrade for another ten Autoconer X5.
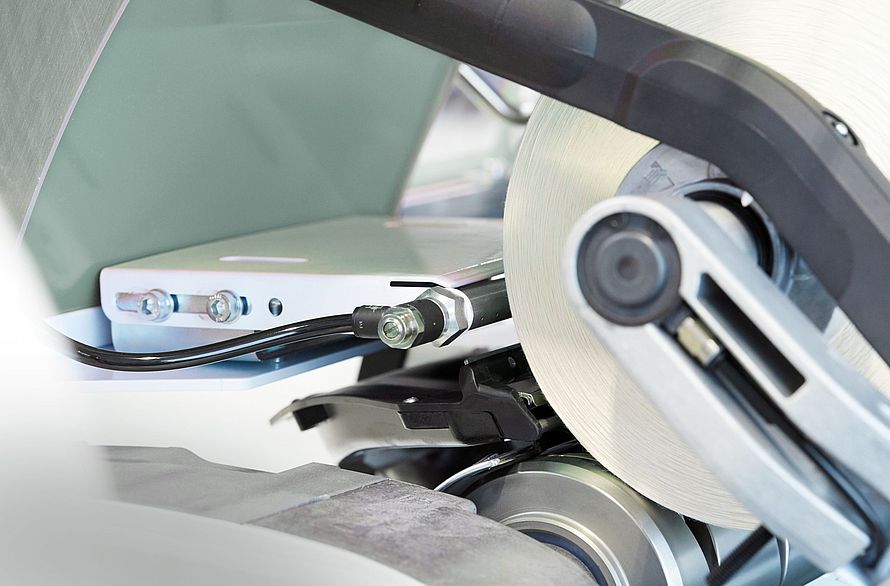
Smartjet helps improve yarn production and reduce labor cost
The Smartjet nozzles had a profound impact on the efficiency, productivity and labor cost of Wugang Longshan Textile’s operations:
- Machine efficiency rose from 80% to 83%, translating to an increase in production to 21 kg per machine per eight-hour shift.
- Annual yarn production expanded by 20 790 kg.
- The demand for manual yarn searching was reduced by 51%, significantly lowering the operators’ workload.
- Operators were able to manage one additional winding machine, thereby reducing labor costs.
- The energy cost per kilogram of yarn was reduced due to increased efficiency.
With the Smartjet nozzle upgrade, not only did production increase, but the need for manual intervention was greatly diminished too. This allowed operators to handle more winding machines simultaneously, effectively lowering labor costs. Additionally, the increased production efficiency led to a reduction in energy consumption per kilogram of yarn produced. These improvements in turn lowered conversion costs which made the customer cost competitive.
The Smartjet nozzle strengthens our market position significantly. It helps reduce operator workload and conversion costs while increasing yarn production. The retrofit of the Smartjet power nozzle on the doffer has been a game-changer for our operations, enhancing our productivity and reducing overall costs.Wang Ping, Chief Engineer at Wugang Yinglong Group.