CROCOdoff Leads to Unique Market Results
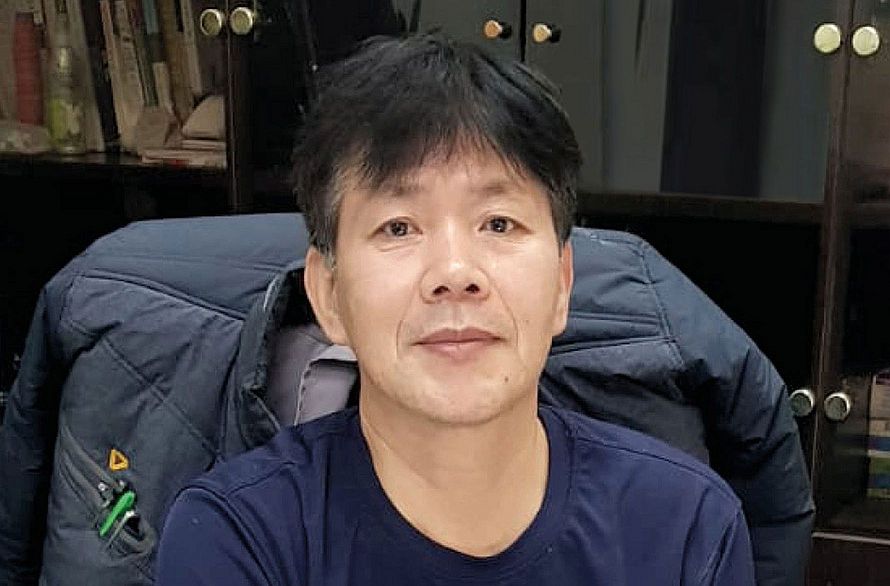
Mr. Kwang Yong Heo, Taekwang Factory Manager
Incorporated in 1950, Taekwang Industrial Co. was the first Korean company to produce acrylic fibers – followed by Spandex, Nylon and Aramid. Today, the company has 10 domestic and overseas locations and its own Research Institute. Within their cotton spinning section, they produce a wide variety of blended yarns of acrylic, polyester and wool, fabricating 15 000 tons of cotton spun yarns annually.
The Challenge
Taekwang has always embraced new technologies to remain at the top of its game. The company wanted to reduce spindle maintenance and improve working conditions at their Banyeo factory. At the same time, Taekwang was looking for solutions to meet the increasing demand for its special yarns.
The Solution
The Banyeo factory runs 80 Zinser ring spinning machines, spinning various raw materials such as polyamide or cotton blends, from coarse to fine yarn counts of Ne 5 to Ne 40. Taekwang opted to upgrade the machines with Novibra NASA HPS 68 spindles with CROCOdoff clamping crowns.
To exploit the maximum CROCOdoff potential, the ring spinning machine needs to be set to less than one turn of the yarn in the underwinding section. With Novibra service engineers unable to enter Korea due to travel restrictions at the time, a 30-minute online training was organized, assisted by the Korean Novibra representative Corvet Tech. Although Taekwang technicians had no experience with an underwinding-free spindle system, this was all that was needed for the team to successfully set up the first machine.
The Customer's Benefits
The first machine running with Novibra spindles and CROCOdoff performed well and offered numerous benefits. The machine runs at 18 500 rpm, spinning 100% combed cotton, Ne 20. Machine operators immediately noticed it was unnecessary to stop the machine for regular monthly cleaning – as was the case with spindles using standard crowns with 3-underwinding system. This saves valuable production time and allows manpower to be deployed elsewhere.
In addition, less operator attendance was required during spinning, as only 25 ends down were reported during the doffing period, instead of 40 before the upgrade.
Another crucial parameter was a 60% reduction of yarn breaks during the spindle start-up after doffing – making a significant difference to efficiency and quality.
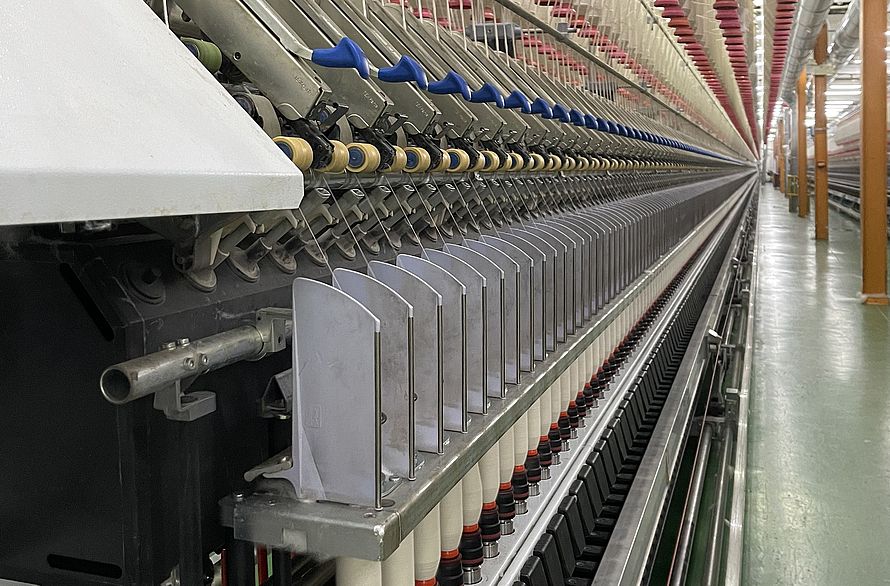
The initial results with Novibra CROCOdoff are very promising and we are very optimistic about the impact this could make across our whole operation.Mr. Kwang Yong Heo, Taekwang Factory Manager