Strong Global Repair Service Footprint
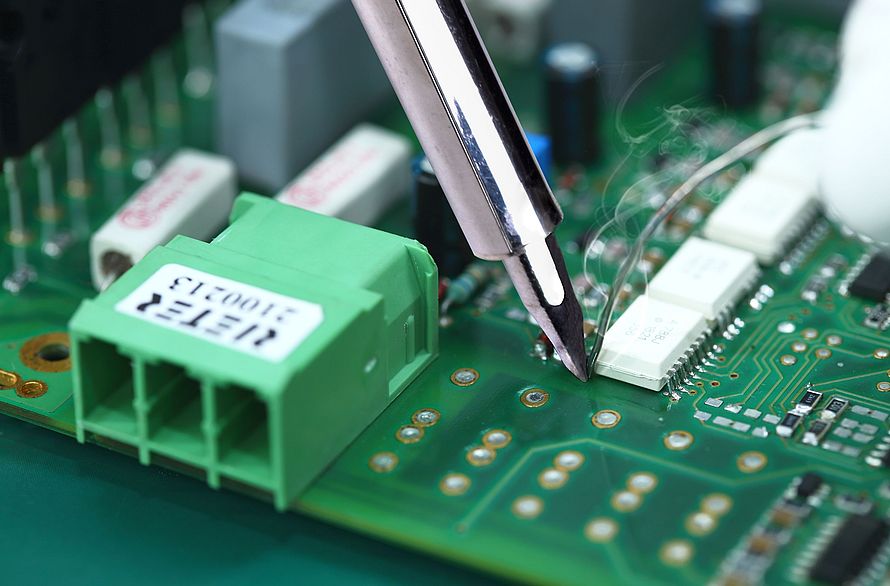
Whenever a textile machine stands still, mill owners lose money. Rieter’s repair service network comprises 25 repair service stations across the globe strategically located on the doorstep of Rieter customers. The network is designed with one goal in mind: providing both mechanical and electronic high-quality repairs at short turnaround time to customers.
Equipped with test equipment designed and manufactured in-house and staffed with certified and experienced engineers, Rieter repair service stations offer all types of repairs, both electronic and mechanical on Rieter machines, from blowroom to winding. Service stations help restore and sustainably maximize the original performance of the machines for Rieter customers. Chen Shun Ming, Chief Engineer at Zhejiang Huzhou Weida Group Co., Ltd., China, says:
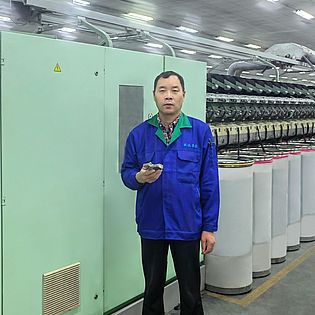
Through a complete refurbishment of the yarn clearer IQ+ of our semi-automated rotor spinning machine BT 923, its functionality was restored to its like-new function.Chen Shun Ming, Chief Engineer, Zhejiang Huzhou Weida Group, China
Aging of parts is inevitable, especially in the high-intensity environment of a spinning mill. Various technological components can be replaced with original parts, a practice that can significantly contribute to the production of high-quality yarn. At Hanif Spinning Mills Ltd., Bangladesh, Mohammed Hanif, Managing Director, described his experience with Rieter’s solution as follows:
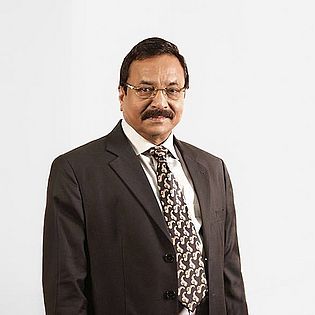
The guiding arm refurbishment and the doffer kit solution offered by Rieter helps us increase production by 10%.Mohammed Hanif, Managing Director, Hanif Spinning Mills Ltd., Bangladesh
High-quality repairs with short turnaround time
Rieter’s 25 repair service stations are spread across the globe, strategically located on the doorstep of Rieter customers. They are equipped with the repair know-how, original spare parts and proprietary test equipment required to validate repairs on Rieter machines.
Certified and experienced engineers offer on-site repairs at customers’ mills and at Rieter’s repair service stations, providing comprehensive service throughout the machine life cycle. This ensures that machines operate at peak performance and downtime is kept to an absolute minimum, ensuring customers stay competitive.
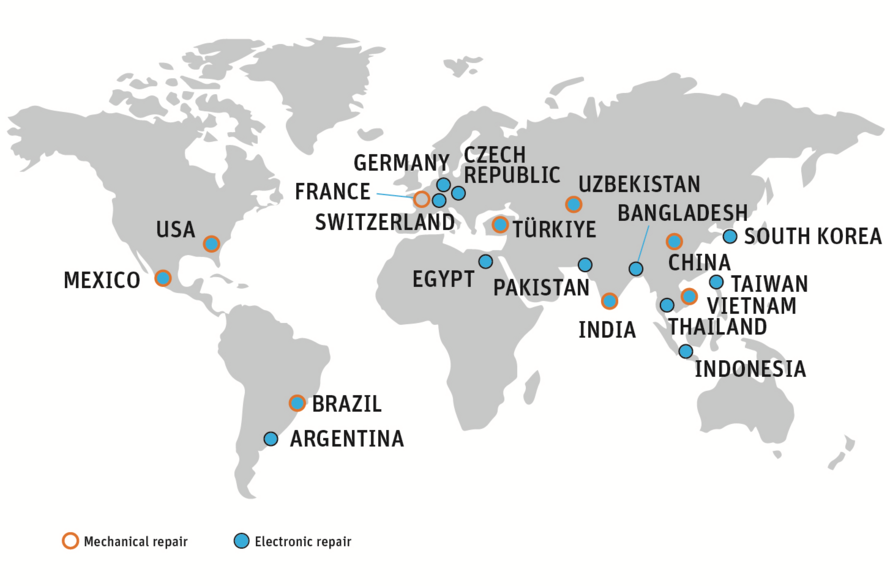