Competitive Advantage with Automated Piecing ROBOspin
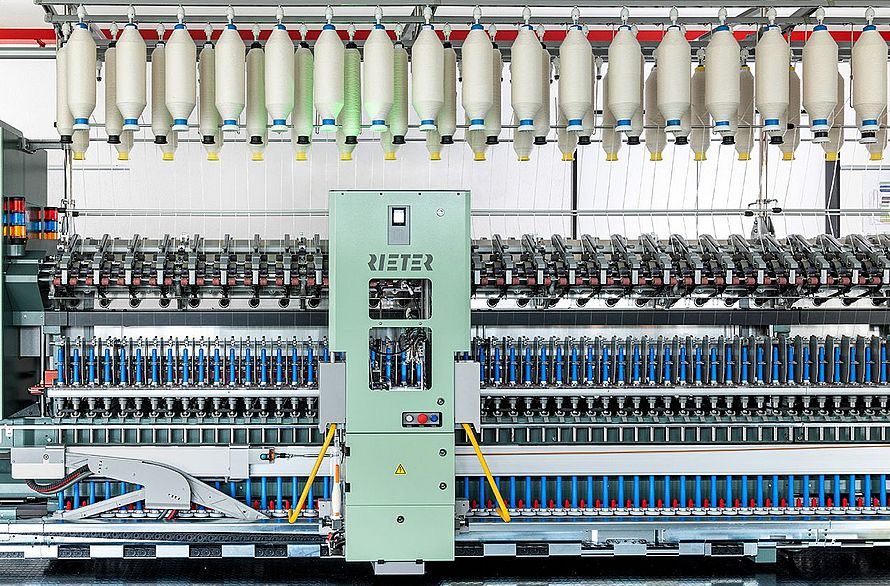
ROBOspin operates 24 hours a day, maintains a consistently high level of productivity, and facilitates the end spinning process for mills.
Each week in spinning mills across the globe, ROBOspin pieces more than 1 000 000 yarn breaks, resulting in a reduction of about 2 000 working hours for operators. In this highly cyclical industry, automation is key for spinning mills to remain competitive. Rieter customers from east to west trust in the automation capabilities of ROBOspin, the industry’s first fully automated piecing robot for ring and compact-spinning machines.
In the competitive world of textile manufacturing, Gildan Yarns, USA, one of the world’s largest vertically integrated manufacturers, continuously embraces the opportunity to enhance ring spinning machine efficiency without compromising on quality. By focusing on innovation and excellence, they adeptly balance reducing operational costs, upholding high standards, and meeting the ever-evolving demands of a dynamic market. With ROBOspin, the industry’s first fully automated piecing robot, Gildan witnessed significant optimizations and automation in the ring spinning process, resulting in cost savings.
Since its launch in spring 2019, Rieter has been selling its piecing robots, designed for Rieter ring and compact-spinning machines, for new machines or as an upgrade for existing machines, to customers from the USA to India.
Rieter’s technology and automation solutions support us in achieving round-the-clock machine availability and flexible personnel management.John Lane, Assistant Plant Manager at Gildan Yarns, USA
Mills trust in Rieter automation technology
By installing ROBOspin, spinning mills around the world reduce their manpower requirements by up to 50% as the robot reliably reaches up to 95% piecing efficiency. ROBOspin significantly reduces the average time for yarn piecing thanks to the Individual Spindle Monitoring system (ISM), which efficiently detects the affected spinning position. The robot travels directly to this position and pieces the yarn break. This results in a significant increase in production output, whether for a major mill like Gildan or a smaller yarn manufacturing plant. Minimal contact with cops means no damage to the outer yarn layer and therefore no contamination of the yarn. As fewer staff are required, the remaining employees benefit from more targeted trainings and more enriching jobs. In addition to the innovative ROBOspin, Rieter provides a suite of tailored solutions including cutting-edge automatic lap transport system SERVOlap, automatic lap change and batt piecing system ROBOlap for combers, automatic roving bobbin transport system SERVOtrail, and advanced automatic doffing solutions for end spinning.
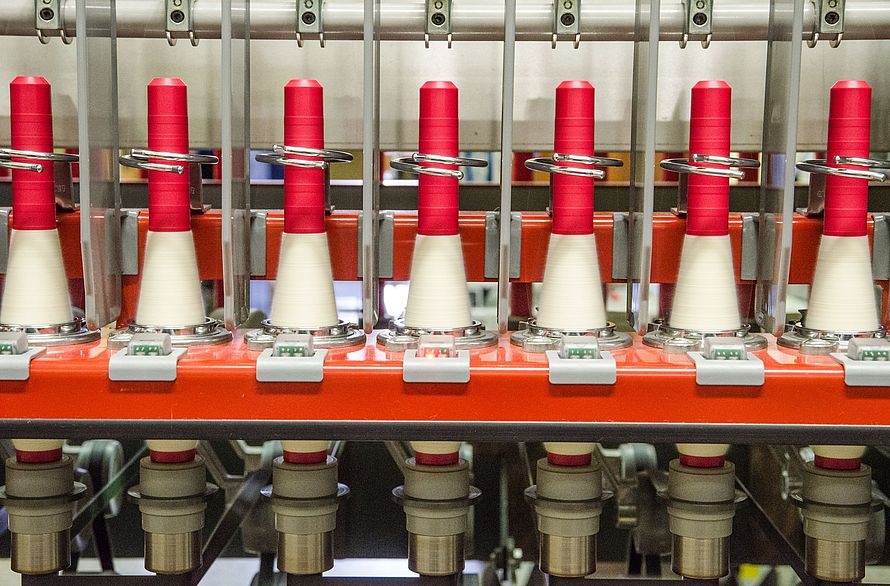
Automated piecing for ring and compact spinning
In spinning mills across the globe, ROBOspin pieces over 1 000 000 yarn breaks every week. This translates into a reduction of about 2 000 working hours per week for operators, which adds up to significant cost savings for customers.
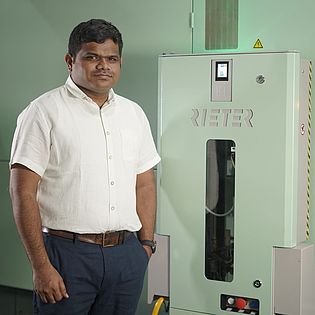
ROBOspin is the perfect automation solution to efficiently schedule the workforce.Durai Arun, Managing Director of Poomex Clothing Company, India
The vertically integrated company is a manufacturer of various types of knitted garments like inner wear for all age groups. They use state-of-the-art spinning processes and the latest technology to produce yarn and garments. ROBOspin was installed at their plant in South India in 2020 on an existing ring spinning machine G 32. “The compact design and consistency in piecing quality are the standout features of this robot,” adds Durai Arun. Since then, Poomex Clothing Company has invested in a ROBOspin for their compact-spinning machine K 42.
The time to transform is now
ROBOspin is having a transformative impact for more and more Rieter customers. With the robots operational round the clock, machine performance remains consistently high while also optimizing productivity. The minimal contact between the robot and yarn preserves quality while ensuring a steady output of high-grade yarn.
Hence, automation is increasingly becoming a decisive competitive advantage for spinning mills across the globe. This is also the case for Uğurlular Textile Industry and Trade Inc., a yarn manufacturer in Türkiye. They ordered piecing robots for more than 30 ring and compact-spinning machines. Uğurlular produces more than 100 tons of yarn daily in its ring, compact- and rotor spinning factories exporting to 30 countries. Automation is what helps them remain competitive and grow profitably.
We believe in investing in technology for a successful future. Rieter convinced us fully with its automation solution for ring yarn piecing that will further support us in growing profitably.Osman Uğurlu, Member of the Board of Directors at Uğurlular Textile Industry and Trade Inc., Türkiye