18% Lower Energy Consumption with Compact-Spinning Machine K 48
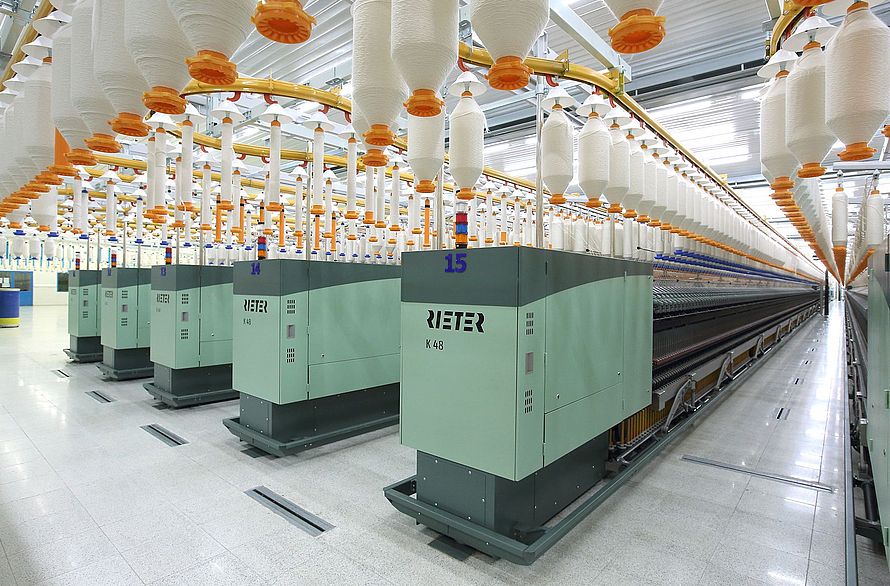
A recent comparison in a Turkish spinning mill shows 18% less energy consumption for the compact-spinning machine K 48 compared to competition. For a machine with 1 824 spindles, this benefit equates to an annual saving of around 12 000 USD per machine. This confirmed once again that Rieter’s compact-yarn technology sets the global benchmark for energy efficiency. These findings are not only crucial for the success of Rieter and its customers, but also contribute to a more sustainable and economical future for the textile industry.
The trials at the Turkish customer were carried out on compact-spinning machines, with spindle speeds at 19 200 rpm to produce 100% cotton compact yarn Ne 30. The figure of energy consumption in kWh per kg yarn is one of the key indicators in spinning mills. The advantage becomes clear with 1.21 kWh/kg for the K 48 versus 1.48 kWh/kg for the competitor machine. This also confirms the result of another comparison with K 48, for a cotton yarn, Ne 40 at 19 500 rpm.
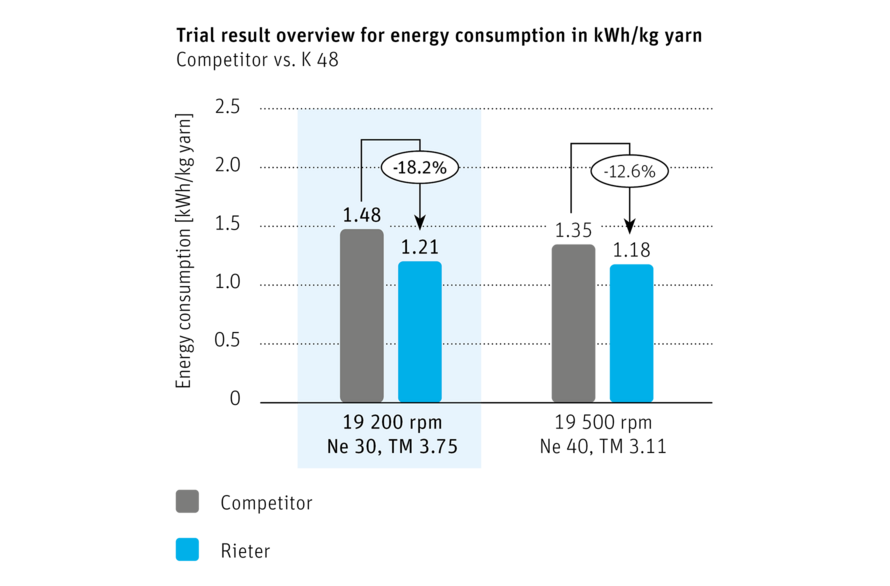
Reasons for This Major Energy Advantage
The largest energy consumers are the spindle drive (75 to 80%) and the suction system (12 to 17%), further drives account for a large proportion of the remaining energy consumption (7 to 10%). The efficient suction system is mainly responsible for the great advantage of Rieter compact-spinning machines. Competitors’ machines all require an additional suction system for the compacting process, which means considerable additional energy consumption. The LENA spindles are also an important feature for lower energy consumption. Their design and efficiency directly impact the kWh per kg yarn, 6% energy saving is possible compared to standard spindles.
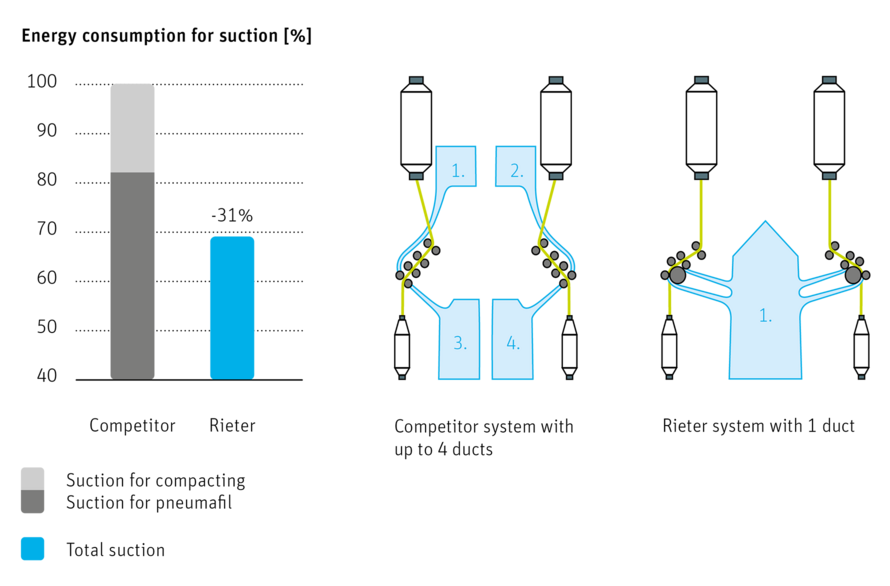
And last, but not least, beyond suction system and spindle dynamics, the efficiency of the main motor drive proves to be an important determinant of energy consumption. Our commitment to optimal energy utilization is underlined by using up to 110 kW big, highly efficient main motors with IE4 technology.
Lower Energy Costs Are Tangible Economic Benefits
For customers, it is more interesting to translate these figures into tangible economic benefits. For a machine with 1 824 spindles, the 18% reduction in energy consumption corresponds to an annual saving of around 12 000 USD per machine (based on energy costs of USD 0.1 per kWh). The lower energy costs make our machines a strategic investment with a tangible return and position Rieter as a market leader in the sustainable production of compact yarns.