Parts that Make a Difference
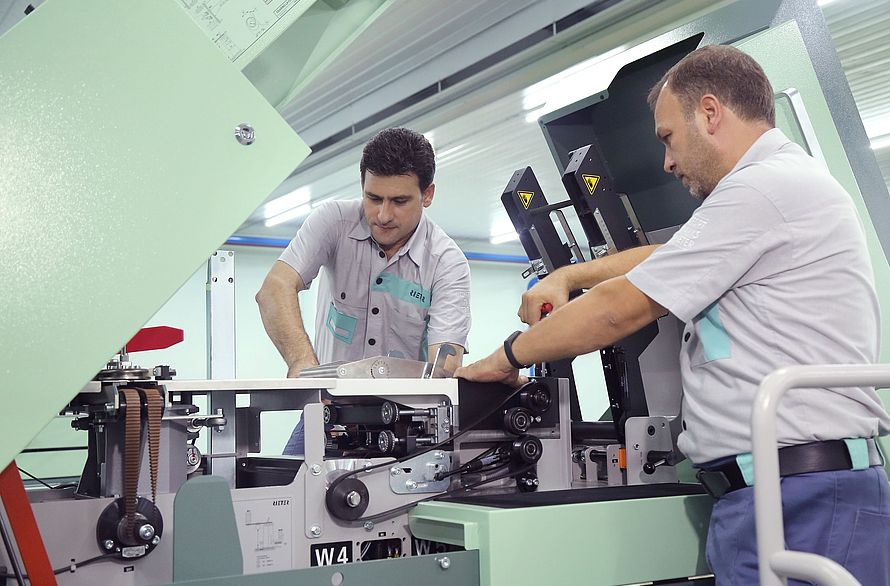
Even the best spinning machines show signs of wear and tear after years of intensive operation. Investing in regular maintenance is smart and helps prevent breakdowns. Rieter maintenance kits combine spare and wear parts with the corresponding service life to improve machine performance and reduce conversion costs.
In today’s fast-paced and technology-driven world, spinning mills rely heavily on continuous machine operation to keep productivity at a high level and reduce conversion costs.
A structured and simple approach
Maintenance budgets are tight and machine downtimes are costly. Rieter’s modular maintenance concept enables spinning mills to follow a structured and simple maintenance approach throughout the product life cycle. It helps with planning the maintenance budget and prevents extended machine downtimes. The maintenance kits consist of key spare parts with a high impact on the machine performance and lifetime. Replacing those parts at the same time not only improves machine performance, but also reduces the overall conversion cost. New spare parts and components ensure that machines retain their key functionality. This also prevents costly repairs in the long term. The maintenance concept comprises three packages: the mini, the performance and the overhaul kit.
Following the proper maintenance procedures yields numerous benefits:
- extended lifetime of the machine,
- enhanced machine performance in terms of productivity and output quality,
- reduced machine downtime,
- improved reliability of the components,
- energy-saving, and
- enhanced safety.
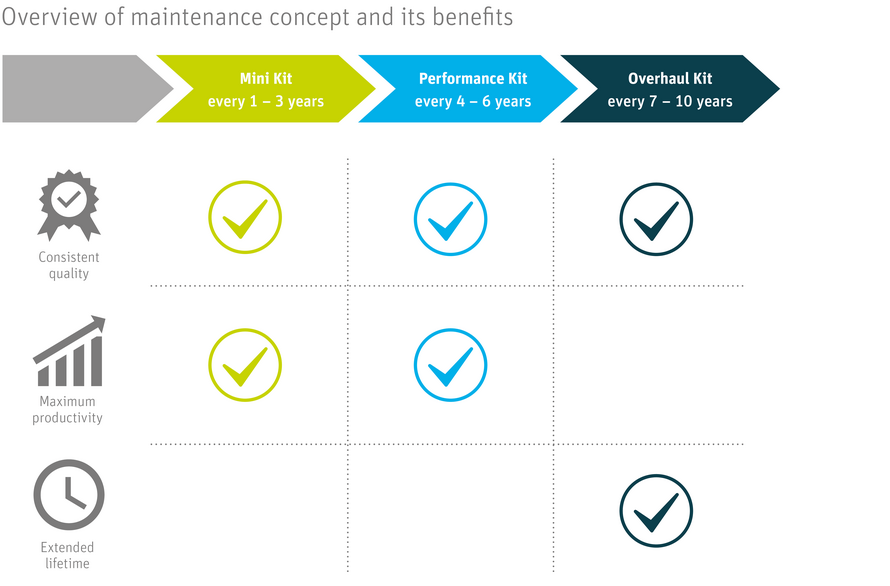
Mini kit supports proper machine functioning
A mini kit consists mostly of technological and consumable parts that have a lifetime of one to three years – depending on the machine group, raw material, operating parameters and general maintenance schedule. Hence, Rieter recommends replacing the mini kit at least every three years. For the card as an example, the implementation of the mini kit leverages the benefits of a new wire in terms of sliver quality. Many additional items such as drive belts or the grinding stone are required to keep the productivity high for longer and support the smooth functioning of the carding machine. These parts can be exchanged during a re-wiring shutdown so that no time is lost for an additional machine stop.
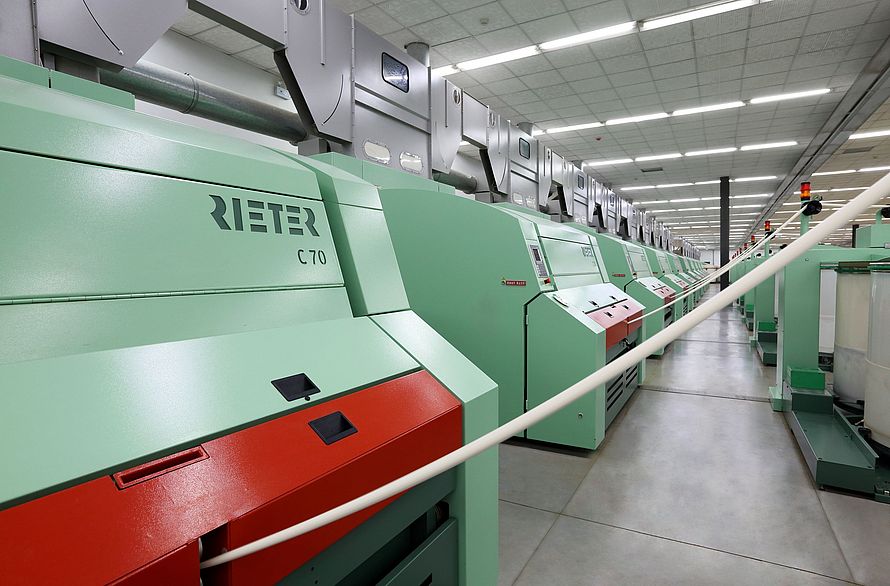
Performance kit ensures smooth operation
The performance kit is designed to ensure the seamless performance of the machine over the next four to six years. This kit consists of bearings, seals, springs, brushes, and many more, to ensure the proper functioning of the drive elements. Changing the parts on the machine can be planned alongside the regular maintenance schedule and is recommended at least every six years. This minimizes machine downtime and maximizes productivity.
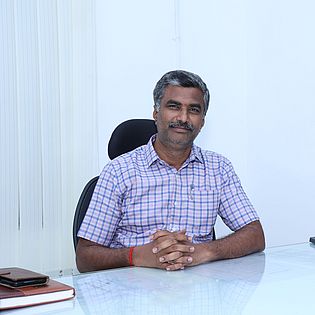
After the installation of the performance kit on the ring spinning machine, we got a substantial improvement in terms of productivity and yarn quality.Anantha Kumar, Factory Manager, Sreedhara Textiles Pvt. Ltd., India.
Preparing for the next decade with the overhaul kit
Even the most robust and sturdy equipment will wear out at some point. Therefore, after seven to 10 years of machine operation, an overhaul of the machine is required, in which metal wearing components are exchanged. The overhaul kit prepares the machine for the next decade of operation. It extends machine lifetime by several years while maintaining its original performance. Essential components support the machine performance. In combination with the mini and performance kits, it can even be used to restore completely worn machines.
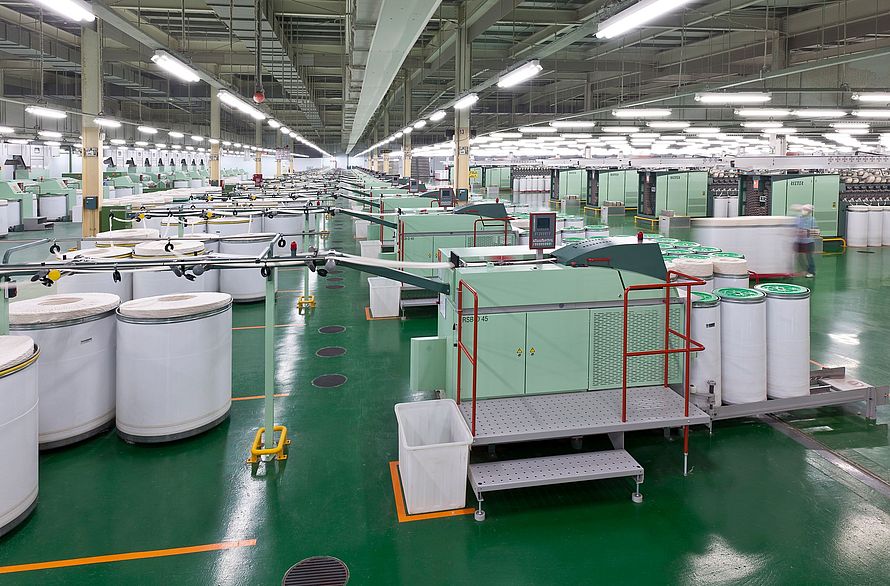
Regular maintenance is the key to success
A well-established machine maintenance practice is indispensable for the success and sustainability of modern businesses. By investing in regular and systematic machine maintenance, customers can benefit from increased operational efficiency, reduced conversion cost and improved quality. It also contributes to a safer and more efficient working environment. Rieter’s online webshop ESSENTIALorder makes ordering these kits and spare parts fast and easy. The system is available 24 hours a day, enabling customers to submit orders from anywhere at any time.